УНІКАЛЬНИЙ СПЕЦІАЛІЗОВАНИЙ ВЕРСТАТ вертикальний трехшпіндельний свердлильно--розточний з рухомим порталом з ЧПУ
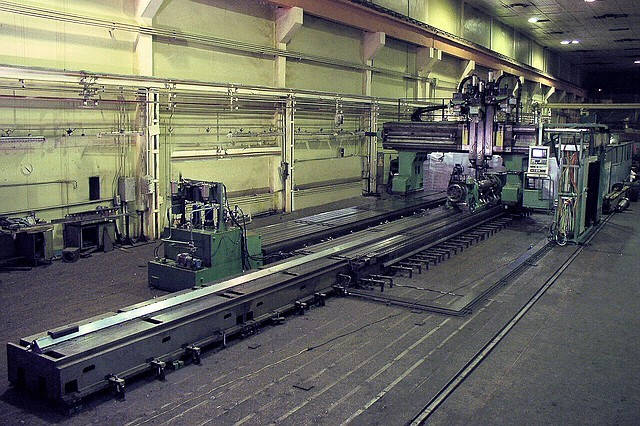
Відкрите акціонерне товариство «Одеський завод радіально-свердлильних верстатів» (ВАТ «ОЗРСС») за проектами Одеського спеціального конструкторського бюро алмазно — розточувальних і радіально — свердлильних верстатів «СКБАРС» з середини 80х років випускає свердлильно-фрезерно-розточувальні верстати з рухомим порталом підвищеної точності з ручною або автоматичною зміною інструменту, керовані системою ЧПУ. Модельний ряд передбачав ширину робочого столу 1250 мм і 2000 мм і хід порталу 4000 мм.
Спеціальні та спеціалізованих вальні верстати, створені на їх базі дозволяли забезпечити высокопроиз-водительную комплексну обробку різних поверхонь великогабаритних деталях машинобудування. Освоєння цього виду продукції стало значним кроком у розвитку вітчизняного машинобудування. У той період за кордоном випуск подібного обладнання освоїли тільки передові фірми — FOREST-LINE Франція, NОVISA Італія, TOS KURIM Чехія та ін
Подальшим поштовхом розвитку цього типу верстатів послужив замовлення Подільського ВАТ «Машинобудівний завод «ЗиО-Подольск», Росія. На тендер, у якому брали участь ряд передових фірм Росії і зарубіжних країн, «СКБАРС» представив розробку спеціалізованого трехшпин-ділового свердлильно - розточувального верстата з рухомим порталом з ЧПУ моделі ОС0000.4037для високопродуктивної многошпиндельной обробки деталей теплообмінного обладнання, основними представниками яких є трубні дошки і колектора. Складність завдання замовника полягала не тільки у вимогах до точност-ним параметрів верстата і необхідності обробки осьових і тангенціальних поверхонь, але і в обов'язковому умови забезпечення на одному верстаті обробки деталей з суперечливими-вимі характеристиками: трубної дошки (співвідношення D:L=16) і кількість лектора (співвідношення D:L=0,045).
Через кілька років напруженої творчої роботи фахівців «СКБАРС», ОЗРСС і Замовника в липні 2004 року унікальний станок випробуваний і зданий комісії.
Оброблювані деталі характеризуються труднообра-батываемым матеріалом — жаростійкі високолеговані сталі.
Найбільша маса трубної дошки 3500 кг, найбільший діаметр оброблюваної деталі 3200 мм, максимальна товщина 200 мм. Діаметр свердління спіральними свердлами в суцільному матеріалі 10...40 мм, максимальний діаметр розсвердлювання, зенкерування 70 мм, максимальний діаметр розточування 40 мм, кількість оброблюваних отворів до 7500 штук.
Найбільша маса трубного кількість лектора 7000 кг, діапазон зовнішніх діаметрів 83...630 мм, діапазон довжин труб 1500...14000 мм, найбільша товщина стінки 75 мм.
Діапазон діаметрів обрабаты-ваемых отворів 10...63 мм, най-більший діаметр розсвердлювання 120 мм.
Оброблювані деталі встановлюються в спеціальних гидрофицированных пристосуваннях на дзеркалі столу. Пристосування для базування і закріплення трубних дощок встановлюються на дзеркалі столу. Пристосування для базування, закріплення і повороту труби колектора складається з приводної і підтримуючої бабок з трехкулачковыми самоцентрирую-летять патронами. Для забезпечення високої точності в ділильної бабці передбачені беззазорные передачі, наявність контролю углово-го позиціонування. Переналагодження пристосування на різні діа-метри труб проводиться знімними змінними елементами, растачивае-ральних безпосередньо на верстаті з використанням оригінальної ос-настки. Переналагодження на різні довжини проводиться переміщенням задньої бабки у відповідне положення. Для зменшення де-формації труби під дією сил різання передбачений спеціальний люнет (підводиться опори), розташований між передньою і задньою бабками. Ділильний механізм встановлюється на нерухомій передньої бабки.
Пристосування для обробки труб колекторів не перешкоджають встановленню на дзеркалі столу трубних дощок. Одночасно по довжині станини можуть бути встановлені дві трубні дошки максимальних габаритів.
Рухливий портал переміщує-ся по осі «Х» («Х1») на LM-напрямних фірми ТНК (Японія), закріплених на станині.
За LM — напрямних (вісь «Y»), закріпленим на фронтальній площині траверси порталу, переміщається каретка з встановленими на ній трьома пинолями. При цьому корпус пінолі «Z» жорстко закріплений на плиті, а корпуси пинолей «Z1» і «Z2» можуть установочно переміщатися уздовж осі «Y» з мінімальним межцен-тровым відстанню 240 мм і максимальним 480мм щодо пінолі «Z» незалежно один від одного. Вертикальна подача по осі «Z», «Z1» і «Z2» здійснює-ся переміщенням пинолей у своїх корпусах незалежно один від одного. Переміщення пинолей і каретки здійснюється за допомогою шарико-гвинтових передач. Примусова зміна інструменту проводиться за показником технологічної стійкості. Переміщення по всіх осях і плавне регулювання числа обертів шпинделя здійснюється цифровими приводами з управлінням від системи ЧПУ моделі SINUMERIK 840D фірми SIEMENS, Німеччина. Обробка трубних колекторів довжиною до 8 м здійснюється повністю за один цикл без переустановлення деталі, а колекторів довжиною понад 8 м здійснюється перевстановлення деталі шляхом повороту її на 180 після повної обробки перше 8м.
Обробка трубних колекторів проводиться жорстко закріпленим шпин-делем №1 (при необхідності можлива обробка будь-яким іншим шпинде-лем).
Обробка трубних дощок проводиться будь-яким набором з трьох шпинделів (три шпинделя одночасно, два будь шпинделя одне-тимчасово, один будь-шпиндель).
Впровадження верстата дозволяє скоротити час обробки однієї трубної дошки з 15 до 6 змін.
На рис.1 і 2 показана обробка сегмента трубної дошки при випробуваннях верстата. На рис. 4 показані передня і задня бабки з затиснутим колектором, а також вузол розвантаження, що дозволяє врівноважити трубу при завантаженні в патрони.
В даний час опрацьовуються технічні завдання на шестишпин-слушну портальний верстат для деталей типу трубна дошка і на портальний верстат, оснащений поворотними кутовими головками для повної механічної обробки деталі «рама візка» залізничних вагонів.
Размеры рабочей поверхности стола, мм, не менее: длина 10000 ширина 3200 Наибольшее расстояние от торцов шпинделей до рабочей поверхности стола, мм 1240 Наибольшее программируемое перемещение рабочих органов по линейным осям, мм портала по оси «X» * 9000 каретки по оси «Y» 3200 пинолей по осям «Z1», «Z2», «Z3» 500 Количество управляемых линейных осей 5 Дискретность задания линейных перемещений, мкм, не более 1 Наибольшее программируемое перемещение рабочих органов по круговым осям, град. 360 Количество управляемых круговых осей («А») 1 Дискретность задания круговых перемещений, градус, не более 0,001 Пределы частот вращения шпинделя, об/мин 15…1500 Пределы рабочих подач, мм/мин: 5…3000 Точность позиционирования по осям X и Y 0,1 Повторяемость 0,04 Установочное перемещение задней бабки 13000 Установочное перемещение шпинделей № 2 и № 3 относительно шпинделя № 1 вдоль траверсы портала по оси «Y» (min/ max межцентровое расстояние), мм 240/480 Мощность каждого привода главного движения, кВт, не менее 12 Габаритные размеры (с отдельно расположенными агрегатами), мм 1) длина 18500 2) ширина 8000 3) высота 4460 Маса (з окремо розташованими агрегатами), кг, орієнтовно 120 000
В. Р. Заремба – Голова правління ВАТ «ОЗРСС» А. В. Собакин –Гл. інженер СКБАРС
ВАТ «ОЗРСС» Україна, 65005, р. Одеса, Вул. Бугаєвська, 21 Тел/факс: (048) 796-51-64 728-67-76 E-mail: rad_goncharov@mail.ru
Размеры рабочей поверхности стола, мм, не менее: длина 10000 ширина 3200 Наибольшее расстояние от торцов шпинделей до рабочей поверхности стола, мм 1240 Наибольшее программируемое перемещение рабочих органов по линейным осям, мм портала по оси «X» * 9000 каретки по оси «Y» 3200 пинолей по осям «Z1», «Z2», «Z3» 500 Количество управляемых линейных осей 5 Дискретность задания линейных перемещений, мкм, не более 1 Наибольшее программируемое перемещение рабочих органов по круговым осям, град. 360 Количество управляемых круговых осей («А») 1 Дискретность задания круговых перемещений, градус, не более 0,001 Пределы частот вращения шпинделя, об/мин 15…1500 Пределы рабочих подач, мм/мин: 5…3000 Точность позиционирования по осям X и Y 0,1 Повторяемость 0,04 Установочное перемещение задней бабки 13000 Установочное перемещение шпинделей № 2 и № 3 относительно шпинделя № 1 вдоль траверсы портала по оси «Y» (min/ max межцентровое расстояние), мм 240/480 Мощность каждого привода главного движения, кВт, не менее 12 Габаритные размеры (с отдельно расположенными агрегатами), мм 1) длина 18500 2) ширина 8000 3) высота 4460 Маса (з окремо розташованими агрегатами), кг, орієнтовно 120 000
В. Р. Заремба – Голова правління ВАТ «ОЗРСС» А. В. Собакин –Гл. інженер СКБАРС
ВАТ «ОЗРСС» Україна, 65005, р. Одеса, Вул. Бугаєвська, 21 Тел/факс: (048) 796-51-64 728-67-76 E-mail: rad_goncharov@mail.ru